L'Istituto di energia solare francese INES ha sviluppato nuovi moduli fotovoltaici con termoplastici e fibre naturali provenienti in Europa, come il lino e il basalto. Gli scienziati mirano a ridurre l'impronta ambientale e il peso dei pannelli solari, migliorando al contempo il riciclaggio.
Un pannello di vetro riciclato sul davanti e un composito di lino sul retro
Immagine: Gd
Dalla rivista fotovoltaica Francia
I ricercatori del National Solar Energy Institute (INES) della Francia-una divisione delle Energie alternative francesi e Atomic Energy Commission (CEA)-stanno sviluppando moduli solari con nuovi materiali a base biologica nei lati anteriori e posteriori.
"Poiché l'impronta di carbonio e l'analisi del ciclo di vita sono ora diventate criteri essenziali nella scelta dei pannelli fotovoltaici, l'approvvigionamento di materiali diventerà un elemento cruciale in Europa nei prossimi anni", ha affermato Anis Fouini, direttore del CEA-ININE , in un'intervista con la rivista fotovoltaica France.
Aude Derrier, il coordinatore del progetto di ricerca, ha affermato che i suoi colleghi hanno esaminato i vari materiali già esistenti, per trovarne uno che potrebbe consentire ai produttori di moduli di produrre pannelli che migliorano le prestazioni, la durata e i costi, abbassando al contempo l'impatto ambientale. Il primo dimostratore è costituito da celle solari eterojunction (HTJ) integrate in un materiale tutto composito.
"Il lato anteriore è realizzato in un polimero pieno di vetro vetro, che fornisce trasparenza", ha detto Derrier. "Il lato posteriore è realizzato in composito basato su termoplastici in cui è stata integrata una tessitura di due fibre, lino e basalto, che fornirà resistenza meccanica, ma anche una migliore resistenza all'umidità."
Il lino proviene dalla Francia settentrionale, dove è già presente l'intero ecosistema industriale. Il basalto proviene altrove in Europa ed è tessuto da un partner industriale di INES. Ciò ha ridotto l'impronta di carbonio di 75 grammi di CO2 per watt, rispetto a un modulo di riferimento della stessa potenza. Il peso è stato anche ottimizzato ed è inferiore a 5 chilogrammi per metro quadrato.
"Questo modulo è rivolto al PV sul tetto e all'integrazione dell'edificio", ha affermato Derrier. “Il vantaggio è che è naturalmente di colore nero, senza la necessità di un foglio di fondo. In termini di riciclaggio, grazie alla termoplastica, che può essere ricordata, la separazione degli strati è anche tecnicamente più semplice. "
Il modulo può essere realizzato senza adattare i processi attuali. Derrier ha affermato che l'idea è quella di trasferire la tecnologia ai produttori, senza ulteriori investimenti.
"L'unico imperativo è avere congelatori per conservare il materiale e non avviare il processo di reticolazione della resina, ma la maggior parte dei produttori oggi utilizza Prepreg e sono già attrezzati per questo", ha detto.
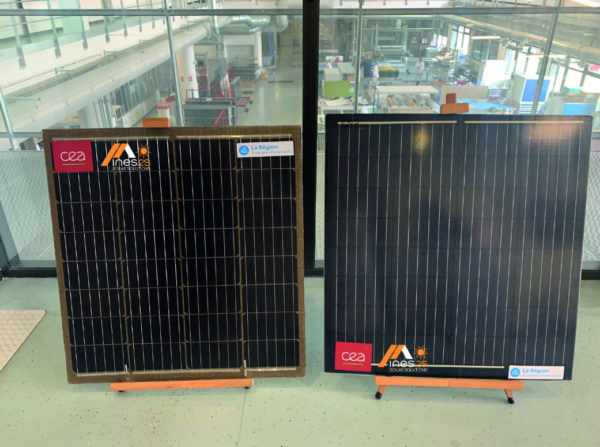
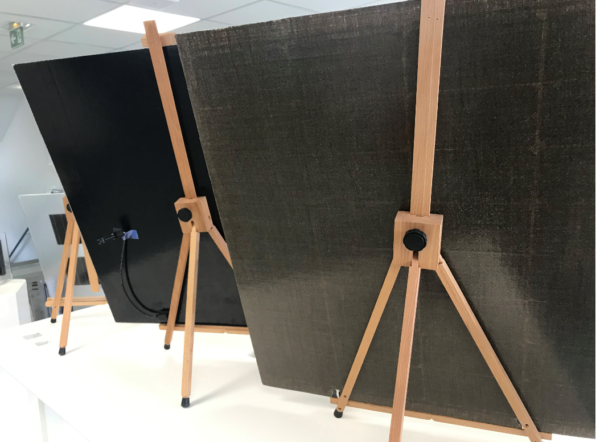
"Abbiamo lavorato alla seconda vita di vetro e sviluppato un modulo composto da vetro da 2,8 mm riutilizzato che proviene da un vecchio modulo", ha affermato Derrier. "Abbiamo anche usato un incapsulante termoplastico che non richiede reticolazione, che sarà quindi facile da riciclare e un composito termoplastico con fibra di lino per la resistenza."
La faccia posteriore senza basalto del modulo ha un colore di lino naturale, che potrebbe essere esteticamente interessante per gli architetti in termini di integrazione della facciata, ad esempio. Inoltre, lo strumento di calcolo INES ha mostrato una riduzione del 10% dell'impronta di carbonio.
"Ora è indispensabile mettere in discussione le catene di alimentazione fotovoltaica", ha detto Jouini. “Con l'aiuto della regione del Rodano-Alpe nel quadro del piano di sviluppo internazionale, siamo quindi andati alla ricerca di giocatori al di fuori del settore solare per trovare nuove termoplastiche e nuove fibre. Abbiamo anche pensato all'attuale processo di laminazione, che è molto ad alta intensità di energia. "
Tra la pressurizzazione, la pressatura e la fase di raffreddamento, la laminazione di solito dura tra 30 e 35 minuti, con una temperatura operativa di circa 150 C a 160 C.
"Ma per i moduli che incorporano sempre più materiali ecologici, è necessario trasformare i termoplastici da circa 200 ° C a 250 ° C, sapendo che la tecnologia HTJ è sensibile al calore e non deve superare i 200 C", ha affermato Derrier.
Il Research Institute sta collaborando con lo specialista di termocompressione a induzione di Francia Roctool, per ridurre i tempi di ciclo e creare forme in base alle esigenze dei clienti. Insieme, hanno sviluppato un modulo con una faccia posteriore fatta di composito termoplastico di tipo polipropilene, a cui sono state integrate le fibre di carbonio riciclate. Il lato anteriore è fatto di termoplastici e fibra di vetro.
"Il processo di termocompressione a induzione di RocTool consente di riscaldare rapidamente le due piastre anteriori e posteriori, senza dover raggiungere i 200 ° C al centro delle cellule HTJ", ha detto Derrier.
La società afferma che l'investimento è inferiore e il processo potrebbe raggiungere un tempo di ciclo di pochi minuti, utilizzando meno energia. La tecnologia è rivolta ai produttori compositi, per offrire loro la possibilità di produrre parti di diverse forme e dimensioni, integrando al contempo materiali più leggeri e più durevoli.
Tempo post: giu-24-2022